Tiểu luận Công nghệ tuyển nổi áp lực trong xử lý nước thải
Bạn đang xem 20 trang mẫu của tài liệu "Tiểu luận Công nghệ tuyển nổi áp lực trong xử lý nước thải", để tải tài liệu gốc về máy hãy click vào nút Download ở trên.
Tóm tắt nội dung tài liệu: Tiểu luận Công nghệ tuyển nổi áp lực trong xử lý nước thải
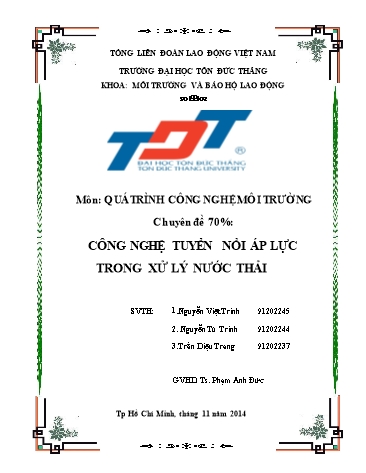
TỔNG LIÊN ĐOÀN LAO ĐỘNG VIỆT NAM TRƯỜNG ĐẠI HỌC TÔN ĐỨC THẮNG KHOA: MÔI TRƯỜNG VÀ BẢO HỘ LAO ĐỘNG & Môn: QUÁ TRÌNH CÔNG NGHỆ MÔI TRƯỜNG Chuyên đề 70%: CÔNG NGHỆ TUYỂN NỔI ÁP LỰC TRONG XỬ LÝ NƯỚC THẢI SVTH: 1.Nguyễn Việt Trinh 91202245 2. Nguyễn Tú Trinh 91202244 3.Trần Diệu Trang 91202237 GVHD: Ts. Phạm Anh Đức Tp Hồ Chí Minh, tháng 11 năm 2014 MỤC LỤC Mở đầu Nguồn nước mặt (sông, hồ, suối) đang và sẽ là nguồn cấp nước chủ đạo hiện nay và trong tương lai cho hệ thống cấp nước ở nhiều đô thị. Quy mô sử dụng nước ngày càng tăng, trong khi chất lượng nước của các nguồn nước mặt lại có xu hướng ngày càng suy giảm do tiếp nhận nhiều nguồn thải khác nhau chảy vào khu vực. Mặt khác tầm quan trọng của vấn đề môi trường tăng cao dẫn đến việc thành lập các tiêu chuẩn môi trường chặt chẽ hơn, tiêu chuẩn này được áp dụng trên ô nhiễm nước thải các ngành công nghiệp. Các công nghệ đang áp dụng hiện nay tại các nhà máy nước, ở cả các quy mô công suất khác nhau, theo cách tiếp cận truyền thống như keo tụ-lắng-lọc nhanh-khử trùng hoặc sơ lắng -keo tụ-lắng -lọc nhanh-khử trùng, chất lượng nước đầu ra của các nhà máy nước ngày càng có nhiều nguy cơ không đáp ứng được tiêu chuẩn và/hoặc phải chịu chi phí xử lý rất tốn kém. Xem xét số lượng lớn các chất thải là điều cần thiết để tìm ra công nghệ mới cao hơn hiệu quả xử lý nước thải để đáp ứng các tiêu chuẩn mới. Những khó khăn và nguy cơ đang đối mặt tại các nhà máy nước có khả năng giải quyết được bằng một số giải pháp công nghệ mới, trong đó có tuyến nổi áp lực thay cho quá trình lắng thông thường. Trên thế giới, công nghệ tuyển nổi áp lực (Dissolved air flotation - DAF) đã được áp dụng tại các trạm xử lý nước cấp và nước thải, xử lý bùn cặn ở nhiều nước, nhằm mục đích nâng cao chất lượng nước sau xử lý và giảm chi phí sản xuất nước cấp, ổn định và làm khô bùn cặn, giảm lượng bùn phải xử lý, vận chuyển, chôn lấp và giảm đáng kể hoá chất tiêu thụ cũng như kích thước các công trình xử lý bùn cặn như sân phơi bùn. Giới thiệu về tuyển nổi áp lực Tuyển nổi áp lực (DAF) đã được sử dụng rộng rãi trong bốn mươi năm qua, loại bỏ được các chất rắn lơ lửng (TSS), các loại dầu và mỡ (O & G), và nhu cầu oxy sinh hóa (BOD) từ nước thải và quá trình công nghiệp khác bằng cách đưa các hạt lơ lửng lên bề mặt chất lỏng. Hệ thống DAF (tuyển nổi không khí hòa tan hay còn gọi là tuyển nổi áp lực) thường được sử dụng để xử lí nước thải sơ bộ, được biết đến như một hệ thống mang tính kinh tế và hiệu quả trong xử lý nước thải công nghiệp. Các hạt rắn, chất béo và các loại vật liệu dầu được hệ thống DAF loại bỏ rất nhanh và bùn thu được từ hệ thống này có tính nhất quán cao. Hệ thống DAF lần đầu tiên được sử dụng để xử lý các bể trong công nghiệp, nơi mà hiện tượng nổi xảy ra. Tốc độ dòng chảy của nước khoảng 2-3 m/giờ (không lớn hơn 5 m/giờ). Hệ thống DAF lần thứ hai được giới thiệu vào năm 1960 và được sử dụng rộng rãi đến ngày nay. Thiết kế của hệ thống DAF này là điển hình của hệ thống trước đó, với tốc độ tải trọng bề mặt dưới 5-7 m/giờ và thời gian keo tụ kéo dài gần 45 phút. Một trong các quá trình của bộ lọc DAF đã được phát triển vào cuối năm 1960, nơi mà tuyển nổi xảy ra trực tiếp trên bộ lọc. Quá trình này được gọi là tuyển nổi không khí hòa tan/ phương pháp lọc (DAFF). Thế hệ thứ ba của hệ thống DAF được phát triển vào năm 1990, ý tưởng hoạt động dựa trên cơ sở DAFF. Tiến bộ gần đây bao gồm các công nghệ như lọc ngược tuyển nổi không khí hòa tan (CoCoDAFF). CoCoDAFF đưa các dòng chảy tuần hoàn trên bộ lọc thông qua số lượng lớn các vòi phun tốc độ dòng chảy thiết kế đặc biệt để phân tán tốt các bọt khí. Một công nghệ khác gần đây gồm DAFRapide, kết hợp giảm thời gian keo tụ với tải trọng bề mặt lên 40 m/giờ và AquaDAF có thể đặt được tốc độ tải trọng bề mặt lên đến 40 m/giờ với tốc độ cao. Các phương pháp tuyển nổi Tuyển nổi với sự tách không khí từ dung dịch Phương pháp này được áp dụng để làm sạch nước thải ô nhiễm. Phương pháp này tạo dung dịch quá bão hòa không khí. Khi giảm áp suất các bọt không khí sẽ tách ra khỏi dung dịch và làm nổi chất bẩn. Tùy thuộc vào biện pháp tạo ra dung dịch quá bão hòa người ta chia ra các loại tuyển nổi sau: Tuyển nổi chân không: Trong tuyển nổi chân không, nước thải được bão hòa không khí ở áp suất khí quyển trong buồng thông khí, sau đó cho vào buồng tuyển nổi trong đó áp suất giữ ở khoảng 225-300 mmHg bằng bơm chân không. Trong buồng tuyển nổi, các bong bong khí rất nhỏ thoát ra làm nổi một phần chất bẩn. Tuyển nổi bơm dâng: Thiết bị bơm dâng được sử dụng để xử lý nước thải trong công nghiệp hóa học. Buồng tuyển nổi phải được bố trí cao. Nước thải Bể tuyển nổi Bồn cao vị Cặn Nước sạch Bình sục khí Không khí Hình 1. Sơ đồ hệ thống tuyển nổi bơm dâng Tuyển nổi áp lực (tuyển nổi khí hòa tan): Phổ biến nhất, làm sạch nước với nồng độ chất lơ lửng cao (4-5 g/l).Tạo ra bọt khí mịn và đều. Tuyển nổi với sự phân tán không khí bằng cơ khí. Sự phân tán khí trong máy tuyển nổi kiểu này được thực hiện nhờ bơm tuabin cánh quạt. Được sử dụng để xử lí nước có nồng độ các hạt keo tụ cao (lớn hơn 2 g/l). Khi cánh quạt quay trong chất lỏng xuất hiện các dòng xoáy nhỏ và tạo ra các bọt khí. Bọt khí càng nhỏ thì quá trình càng hiệu quả. Thông thường máy tuyển nổi gồm một số buồng mắc nối tiếp. Đường kính cánh quạt 600-700mm. Hiện nay người ta dùng các máy tuyển nổi cơ khí được sản xuất đại trà trong tuyển nổi quặng để xử lý nước thải. Như vậy thiết kế của các cánh khuấy và thông số hoạt động không tối ưu khi xử lý nước thải. Để tuyển nổi nước thải cần đề xuất một thiết kế tuyển nổi mới có xét đến những tính đặc hiệu của quá trình : chất ô nhiễm bị phân tán, năng suất tạo bọt thấp (1-5%)và cần loại bỏ hoàn toàn các thành phần nhiễm bẩn. Tuyển nổi nhờ các tấm xốp Khi cho khí qua các tấm sứ xốp sẽ thu được bọt khí có kích thước bằng: R=64σr2 R, r :bán kính bong bóng khí và lỗ :sức căng bề mặt của nước Hiệu suất tuyển nổi phụ thuộc vào lỗ, áp suất không khí, lưu lượng không khí, thời gian tuyển nổi, mực nước trong các thiết bị tuyển nổi. Hình 2. Sơ đồ tuyển nổi nhờ các tấm xốp Tuyển nổi hóa học. Trong quá trình xử lý nước có thể diễn ra các quá trình hoá học với sự phát sinh các khí khác như: O2, CO2,Cl2bọt của các khí này có thể kết dính với các chất lơ lửng không tan và đưa chúng lên lớp bọt. Ít được sử dụng nhiều trong công nghiệp. Tuyển nổi sinh học. Phương pháp này dùng để nén cặn từ bể lắng đợt 1 khi xử lý nước thải sinh hoạt. Trong phương pháp này cặn được đun nóng bằng hơi nước đến 35- 550C và nhiệt độ này được giữ vào ngày đêm. Do hoạt động của các vi sinh vật các bọt khí sinh ra và mang các hạt cặn lên lớp bọt, ở đó chúng được nén và khử nước. Bằng cách này 5- 6 ngày đêm độ ẩm của cặn có thể giảm đến 80% và tiếp tục quá trình xử lý cặn tiếp theo. Tuyển nổi điện hóa Khi có dòng điện đi qua chất lỏng, hydro được giải phóng ở catot và oxy ở anot. Khác với những phương pháp làm thoáng dùng không khí để tuyển nổi, trong phương pháp điện hoá khí là hydro là chất tuyển nổi tích cực. Trong tuyển nổi điện hoá, khí được tạo ra dưới dạng những bong bóng cực kỳ nhỏ kích thước 20 micromet, ở anot oxy được giải phóng góp phần oxy hóa các chất hữu cơ. Trong nước trung tính, kiềm yếu sự ăn mòn mạnh mẽ các kim loại ở anot xảy cùng với sự tạo thành của hidroxide, hấp thụ một phần chất hữu cơ sau đó được tuyển nổi nhờ hidrogen và được loại khỏi nước dưới dạng bọt. Do dó người ta còn gọi quá trình xử lý điện hóa với anot là loại tuyển nổi – keo tụ điện hay tuyển nổi bông điện. Những yếu tố này cho phép xử lý ở tốc độ rất cao. Nồng độ tồn dư của các hạt keo tụ trong nước thải từ nhà máy có thể giảm còn 2-3 mg/l sau khi tuyển nổi điện hóa. Tuyển nổi tự nhiên Tuyển nổi tự nhiên thường dùng trong tất cả các quá trình loại bỏ sơ bộ dầu mỡ phương pháp này( hai pha) có thể tiến hành trước sự hợp tính( cho phép liên kết các hạt nhỏ)để đạt được một kích thước nhỏ nhất. Tuyển nổi tự nhiên có thể sinh ra khí do quá trình lên men, đó là trường hợp của“mủ bùn” của công trình tiêu bùn có nồng độ MS từ 20 – 40%, do đó tỷ trọng chỉ có 0,7 –0,8 Kg/l. Tuyển nổi áp lực ( tuyển nổi bọt khí nhỏ ) Nguyên lý chung. Trong các loại tuyển nổi thì tuyển nổi áp lực được ứng dụng rộng rãi hơn cả vì có khả năng tạo ra các bọt khí có kích thước nhỏ (40-70µm) và dễ dàng phân phối đều trong toàn bộ khối lượng nước cần xử lý. Tuyển nổi áp lực (DAF) là một quá trình loại bỏ các hạt lơ lửng trong chất lỏng bằng cách đưa các hạt lơ lửng lên bề mặt chất lỏng. Chất lỏng chảy đến có thể là nước thô, nước thải hoặc bùn lỏng. Hệ thống tuyển nổi bao gồm bốn thành phần chính: cung cấp không khí, máy bơm áp suất cao, bình áp lực (bể lưu giữ) và buồng tuyển nổi. Theo định luật Henry, độ hòa tan của khí trong dung dịch nước tăng khi áp lực ngày càng tăng. Không khí được hòa tan trong nước thải ở áp suất cao trong bình áp lực, và các bọt khí nhỏ được hình thành khi trong nước xuất hiện những bọt khí ở áp suất khí quyển. Nguồn nước cung cấp đến có thể được nén bằng một máy bơm áp lực từ 172 đến 620 kPa với khí nén thêm vào bơm hút. Dòng áp lực được đưa vào bình lưu giữ ở áp suất cao khoảng 0.5 đến 30 phút cho phép đủ thời gian để hòa tan không khí vào dòng nước thải. Sau đó dòng nước được đưa qua một van giảm áp để vào buồng tuyển nổi. Kết quả của việc giảm đột ngột áp lực trong buồng tuyển nổi là sự tạo thành các bọt khí nhỏ. Các bọt khí nhỏ bám dính vào các hạt cặn lơ lửng hoặc các hạt keo trong nước cho đến khi lực đẩy nổi của nước tăng sẽ đưa hỗn hợp khí-cặn lên trên bề mặt tạo thành một lớp váng. Tỷ lệ tăng theo chiều dọc của bọt khí dao động từ 0.152 đến 0.061 m/phút. Các máy cào hoặc thiết bị gạn bọt khác tiếp tục loại bỏ các váng bọt nổi trên bề mặt. Dòng thải của DAF được rút ra từ đáy bể tuyển nổi để tái sử dụng hoặc thải bỏ. Hình 3. Tuyển nổi không khí hòa tan toàn dòng chảy Hình 4. Tuyển nổi áp lực một phần dòng chảy không tuần hoàn Hình 5. Tuyển nổi áp lực có tuần hoàn dòng chảy Ba cấu hình hoạt động có sẵn của hệ thống DAF bao gồm: Tuyển nổi áp lực toàn dòng chảy, nơi mà toàn bộ dòng chảy đến được bão hòa và đưa vào buồng tuyển nổi khi các bọt khí được hình thành (Hình 3). Quá trình này thường được áp dụng cho dòng nước thải có hàm lượng chất rắn lơ lửng vượt quá 800 mg/l, mà không cần keo tụ nhưng đòi hỏi một lượng lớn bọt khí. Tuyển nổi áp lực mà một phần dòng chảy không có hệ thống tuần hoàn, một phần được đưa trực tiếp vào bể tuyển nổi (khoảng 30-50%). Phần còn lại của dòng chảy được cung cấp bởi máy bơm trọng lực với áp suất thấp để vào bể tuyển nổi (Hình 4). Sơ đồ này được sử dụng trong loại bỏ các chất lơ lửng ở nồng độ thấp và yêu cầu không khí thấp. Tuyển nổi áp lực có tuần hoàn dòng chảy, nơi một phần nước thải sau khi xử lý (khoảng 15-20%) được tuần hoàn trở lại bể tuyển nổi (Hình 5). Quá trình này thường sử dụng khi keo tụ tạo bông là một phần của hệ thống xử lý. Lựa chọn này phổ biến nhất trong xử lý nước thải bao gồm việc loại bỏ dầu. Các giai đoạn trong tuyển nổi áp lực. Hình 5. Sơ đồ của quá trình tuyển nổi không khí hòa tan để xử lý nước Chuyển không khí sang mặt phân chia khí-nước trong bình bão hòa. Sự phân tán khí, hòa tan không khí vào trong nước. Không khí trong trạng thái hòa tan “kết tủa” để tạo thành bọt khí. Kết dính các bọt khí. Sự vận chuyển các bọt khí đến các hạt rắn để tạo được “mối liên hệ” và “sự dính bám” . Tuyển nổi hỗn hợp của các bọt khí-hạt rắn trong buồng tuyển nổi. Tách cặn ra khỏi nước trong bể tuyển nổi. Chuyển không khí sang mặt phân chia khí-nước trong bình bão hòa: Chuyển không khí theo đường ống hút của bơm Khí + nước Nước Khí Hình 6. Sơ đồ cấp khí theo đường ống hút của bơm Khi đưa khí vào phía trước bơm sẽ tăng cường khả năng làm nhỏ bong bóng khí trong bơm. Tuy nhiên làm giảm công suất và áp lực của bơm,chế độ làm việc của bơm sẽ không được tốt. Chuyển không khí theo đường ống có áp của bơm Khí + Nước Khí Nước Hình 7. Sơ đồ cấp khí theo đường ống có áp của bơm Để cho nước không rơi vào ống đưa khí vào phải làm thêm van một chiều. Dùng ejector Khí+ Nước Khí Nước Hình 8. Sơ đồ ejector Hai sơ đồ 7 và 8 được ứng dụng trong trường hợp các chất lơ lửng trong nước có kích thước lớn. Sự dao động mực nước trong bể tiếp nhận làm ảnh hưởng đến chế độ bơm, do đó mực nước trong bể không được thấp hơn 0,5m và thường dao động trong khoảng 1,5 – 2m. Để bảo đảm mực nước này, có thể hoàn lưu trở lại bể tiếp nhận một ít nước sau xử lý khi cần thiết. Quá trình phân tán, hòa tan không khí vào nước. Hiệu quả tuyển nổi phụ thuộc vào lưu lượng khí hoà tan trong nước và lượng bọt khí thoát ra từ dung dịch quá bão hoà. Cân bằng pha khí chuyển sang pha nước được đưa ra bởi định luật Henry. Định luật Henry khẳng định rằng nồng độ dung dịch nước của khí hòa tan tỷ lệ thuân với áp suất riêng phần của khí. CA=H.xA.PT Trong đó: CA: nồng độ của không khí hòa tan A trong dung dịch nước (kg/m3) H: hằng số Henry (kg/m3/kPa) XA: phần mol khí trong pha khí PT: áp suất tổng của tất cả các pha (kPa) Nồng độ không khí hòa tan khi ra khỏi bình áp lực thường thấp hơn so với mức độ cân bằng như định luật Henry đã khẳng định. Tỷ lệ của hai giá trị là yếu tố hiệu quả. Do đó có sự thay đổi trong định luật Henry cho bình áp lực: CA=f.H.xA.PT Trong đó f= tỷ lệ nồng độ khí ra khỏi bình áp lực với tỷ lệ nồng độ khí được dự đoán bởi định luật Henry. Sự hình thành bọt khí từ dung dịch quá bão hòa. Các bọt khí nhỏ, 100µm hoặc ít hơn, được hình thành bằng cách bơm nước tuần hoàn quá bão hòa dưới áp lực vào trong bể tuyển nổi bằng vòi phun thiết kế đặc biệt, sự chênh lệch áp suất lớn trên vòi phun tạo ra các bọt khí một cách tự nhiên. Bọt khí phát triển cố định do không khí di chuyển trong nước. Khi không khí thừa được chuyển từ pha khí để được hòa tan, các bong bóng phát triển với các kích thước. Sự tăng trưởng các bọt khí có thể xảy ra do sự tăng hoặc giảm áp suất thủy tĩnh hoặc sự kết dính. Các phép đo kích thước của bọt khí cho hệ thống DAF chỉ ra rằng bọt khí duy trì một phạm vi kích thước trạng thái ổn định từ 10-100µm. Ước tính hợp lý cho kích thước của bọt khí là 40 µm. Trạng thái ổn định phụ thuộc vào áp lực của bình áp lực và tốc độ dòng chảy. Sự phun phải diễn ra một cách nhanh chóng dưới áp suất thấp và có đủ để ngăn chặn dòng chảy và sự tăng trưởng bọt khí trên bề mặt trong vùng lân cận của hệ thống phun. Để đảm bảo bọt khí nhỏ, sự chênh lệch áp lực được khuyến khích từ 400 đến 600 kPa. Theo định luật Henry, giảm áp suất hoặc tăng nhiệt độ khí sẽ tách ra khỏi nước. Kích thước nhỏ nhất Rmin của bọt khí phụ thuộc vào lực căn bề mặt khí – nước và độ giảm áp lực : Rmin = 2 𝜎 /(P-P1), (mm). Trong đó: : lực căng bề mặt khí – nước P : áp suất bão hoà (Pa) P1 : áp suất trong bình tuyển nổi (Pa). Bọt khí và chất rắn va chạm và dính bám nhau trong vùng trộn. Có ba cơ chế để hình thành hỗn hợp khí-rắn: Các bong bóng hình thành trước trong cấu trúc cụm xốp lớn (kích thước cụm xốp lớn hơn nhiều so với quy mô kích thước của bọt khí) Sự tăng trưởng bọt khí trong các hạt hoặc trong cụm xốp Va chạm và bám dính bọt khí vào các hạt. Đối với quá trình DAF, cơ chế thứ ba là quan trọng nhất. Góc tiếp xúc giữa các hạt và bọt khí được sử dụng để mô tả mức độ bám dính của bọt khí. Ở đây góc tiếp xúc phải là hữu hạn và đủ lớn để năng lượng bám dính vào nước của các hạt rắn là nhỏ hơn năng lượng gắn kết của nước. Một góc tiếp xúc lớn hơn cho cả hai kỵ nước và dính ướt tốt. Tuy nhiên, độ lớn của góc tiếp xúc phụ thuộc vào kích thước của bọt khí và hạt. Một quan điểm khác của sự bám dính giữa hỗn hợp khí- cặn bởi bọt khí nhỏ là một góc tiếp xúc hữu hạn không cần phải hình thành. Đối với các hạt kỵ nước có thể tăng lên bằng cách giảm điện tích âm. Các hạt khác, chẳng hạn như kết tủa hoặc Al(OH)3, có sự phân cực và làm cho nó thấm nước. Hiệu ứng thấm nước này có thể giảm sự trung hòa, nhưng hạt nhôm hydroxit có một lớp phủ polymolecular thấm nước nên cản trở bong bóng bám dính. Sự dính kết bọt khí ảnh hưởng đến số lượng và kích thước bọt khí, nên sẽ gây ra ảnh hưởng đến quá trình tuyển nổi. Sự dính kết các bọt khí có thể xảy ra trong nước, trong lớp bọt tạo thành của quá trình tuyển nổi. Đôi khi sự dính kết làm tăng hiệu quả của quá trình tuyển nổi, nhưng thường nó làm cản trở quá trình này. Các hạt có kích thước nhỏ khó nổi lên bề mặt, các hạt có kích thước lớn hơn lại tham gia quá trình tuyển nổi. Mặt khác sự dính kết bọt khí làm giảm diện tích bề mặt và thời gian lưu của bọt khí trong bể. Do vậy trong quá trình tuyển nổi cần hạn chế tối đa các ảnh hưởng xấu do sự dính kết bọt khí gây ra. Sự vận chuyển các bọt khí đến các hạt rắn để tạo được “mối liên hệ” và “sự dính bám” . Khả năng hình thành các keo khí phụ thuộc vào bản chất hạt cặn và có thể phân chia thành ba dạng: Các hạt cặn va chạm vào bọt khí và dính bám. Các bọt khí phát sinh trong lớp cặn lơ lửng. Đầu tiên trong lớp cặn hình thành các bọt khí nhỏ, sau đó chúng va chạm và dính bám với nhau tạo thành các bọt khí lớn có đủ khả năng tuyển nổi. Đối với hiệu quả khu vực phản ứng (dNfl/dt) được xác định là sự giảm số lượng của cụm xốp với thời gian, kích cỡ cụm xốp và bọt khí (dfl và db) và nồng độ được định nghĩa là thông số quá trình có liên quan: dNft/dt = - (3/2)(αpbηT)(ΦbνbNfl)/db Trong đó: αpb : hiệu quả bám dính ηT : tổng thu hiệu quả nhất db : đường kính bọt khí νb : tốc độ gia tăng của bọt khí Nfl : nồng độ cụm xốp Φb : nồng độ khối lượng bọt khí Sự bám dính hỗn hợp khí-cặn được coi là cơ chế động học phù hợp nhất cho hiệu quả của DAF, tùy thuộc vào kích thước cụm xốp và bọt khí (dn và db), và sự kết hợp ở ηT. Tốc độ vận chuyển không khí: Sự vận chuyển khí trong một pha để hòa tan khí tỷ lệ thuận với độ thiếu hụt của bình áp lực. dCdtr=KLa(CS-C) Trong đó: dCdtr= tốc độ thay đổi nồng độ khí hòa tan (kg/m3/s) t = thời gian trôi qua (s) KLa: hệ số chuyển đổi khối lượng (s-1) CS: nồng độ bão hòa (kg/m3) C: nồng độ khí hòa tan trong một pha ở thời gian t (kg/m3) Hệ số chuyển đổi khối lượng KLa = (D/δ) (A/pha khí nước)/V(bình áp lực) Trong đó D= liên tục khuếch tán không khí hòa tan trong nước (m2/s) δ : độ dày màng (m). A (pha khí nước) = diện tích bề mặt khí nước trong bình áp lực (m2). V (bình áp lực) = thể tích của bình áp lực (m3). Quá trình tách cặn ra khỏi nước trong bể tuyển nổi Tách cặn ra khỏi nước trong bể tuyển nổi xảy ra theo hai chiều ngược nhau. Hỗn hợp cặn khí nổi lên trên, nước trong đi xuống dưới để vào máng thu dẫn ra ngoài. Vận tốc nước đi xuống hay tải trọng bề mặt của bể tuyển nổi và lượng cặn được tách ra phụ thuộc vào tính chất của cặn và tỷ số: AS=Trọng lượng không khí hòatantrong nướcTrọng lượng cặn được tách ra khỏi nước Trong xử lý nước thường nước nguồn có chứa cặn thô những hạt cặn nặng, chắc, diện tích bề mặt không phát triển thường không bị đẩy lên bề mặt mà lắng xuống đáy bể, ví vậy bể phải cấu tạo hố thu cặn và thiết bị xả cặn. Tiểu chuẩn thiết kế bể tuyển nổi lấy trong giới hạn: - Tải trọng bề mặt : 3 – 10m3/m2h. - Thời gian lưu nước trong bể: 20 – 40 phút. - Lượng không khí tiêu thụ : 15 – 50 lít/ m3 nước. - Cấu tạo bể tuyển nổi: + Bể tuyển nổi có bề mặt hình chữ nhật + Bể tuyển nổi hình tròn - Chiều cao ngăn tạo bọt Hk = 1,5m. - Đường kính ngăn tạo bọt: Dk=0,6 QVk Trong đó: Q: Lưu lượng nước xử lý (m3/h) vk: vận tốc nước trong ngăn, lấy 6 mm/s 0,6: hệ số đổi đơn vị Thời gian lưu nước trong ngăn 4 –6 phút. Chiều cao vùng lắng H0 = 1,5m, tổng chiều cao của bể H⏀= 3m. Đường kính của bể: D∅=4Qt0πH∅60 Trong đó: to: thời gian lưu nước trong bể từ 20-40 phút Các yếu tố ảnh hưởng đến hiệu suất của quá trình tuyển nổi Keo tụ và tạo bông Hàm lượng nước thô Tốc độ dâng lên của hạt Tỷ lệ khí-rắn Tốc độ tải trọng thủy lực Tốc độ tải trọng rắn Tỷ số tuần hoàn Keo tụ và tạo bông Keo tụ là quá trình gây mất ổn định các hạt keo nhằm tăng sự va chạm của các hạt để xuất hiện các hạt keo lớn hơn. Chất keo tụ là một hóa chất được thêm vào để làm mất đi độ bền của các hạt keo và hỗ trợ sự hình thành bông cặn. Keo tụ là quá trình mang lại những va chạm giữa các hạt lơ lủng mất ổn định và chất keo tạo thành các hạt lớn hơn có thể loại bỏ dễ dàng. Keo tụ và tạo bông là cơ chế mà các hạt lơ lửng và vật liệu dạng keo được loại bỏ khỏi nước trong quá trình tuyển nổi. Tối ưu hóa keo tụ-tạo bông là chần thiết cho hiệu suất tối ưu của hệ thống tuyển nổi. Định lượng loại và lượng hóa chất, cường độ khuấy trộn, thời gian lưu trong vùng trộn, vùng tạo bông và kích thước bông cặn là thông số đóng vai trò quan trọng trong việc thực hiện của hệ thống tuyển nổi. Tỷ lệ khí-rắn (A/S) Tỷ lệ khí-rắn là tham số thiết kế chính cho một hệ thống tuyển nổi không khí hòa tan. Nó là thước đo tiêu chuẩn của trọng lượng không khí hòa tan trong nước trên trọng lượng chất rắn được loại bỏ khỏi nước. Giá trị thông thường 0.005 – 0.06 ml/mg. Đối với bình không khí bão hòa, mối quan hệ giữa tỷ lệ khí-rắn, độ hòa tan không khí, áp suất vận hành, nồng độ chất rắn, tốc độ dòng chảy và tỷ số tuần hoàn được cho bởi phương trình sau: A/S=1.3 ×Sa ×(fP-1)×RSS×Q Trong đó: A/S: tỷ lệ khí-rắn, ml(không khí)/mg(chất rắn) 1.3: trọng lượng không đổi của không khí, mg/ml Sa: hệ số tan của không khí trong nước, ml/l F: phần bão hòa, thường là 0.5 P: áp suất hệ thống tuần hoàn, atm Ss: buồng chứa chất rắn lơ lưng, mg/l R: tốc độ tuần hoàn dòng chảy áp lực, m3/ngày đêm Q; tốc độ dòng chảy nước thô, m3/ngày đêm Tỷ số tuần hoàn Tỷ số tuần hoàn là phần cuối cùng của nước thải được trả về và bão hòa với không khí chịu áp lực trước khi vào bể tuyển nổi nơi áp suất giảm đột ngột gây ra sự xuất hiện của các bọt khí nhỏ. Phạm vi tỷ số tuần hoàn là từ 8% đến 150% dựa trên chất lượng nước thô được xử lý. Theo định luật Henry, tỷ lệ không khí hòa tan tỷ lệ thuận với áp suất tuyệt đối riêng phần của các khí tiếp xúc với chất lỏng. Do đó, cao hơn áp suất vận hành của máy bơm DAF hoặc bình không khí/ độ bão hòa nước, tăng khả năng hòa tan không khí, do đó hạ thấp yêu cầu tỷ số tuần hoàn. Tốc độ tải trọng thủy lực Tốc độ tải trọng thủy lực là một phép đo khối lượng của nước thải được áp dụng hiệu quả trên một đơn vị diện tích bề mặt trên một đơn vị thời gian. Kết quả là con số quá trình thiết kế thể hiện như vận tốc dâng lên tương đương với các đơn vị m/giờ. HLR tùy thuộc các yếu tố khác nhau, tuy nhiên nó dao động từ 4 đến 12 m/giờ. HLR tối đa phải nhỏ hơn tốc độ tăng tối thiểu của các hạt rắn-khí để đảm bảo rằng tất cả các hạt sẽ nổi lên mặt nước trước khi đi đến chỗ tháo nước cuối cùng của bể. Tốc độ tải trọng thủy lực được kiển tra dựa trên tốc độ dòng chảy đến và tổng số tốc độ dong chảy (dòng chảy đến+tuần hoàn Công nghiệp Tốc độ tải trọng thủy lực Nhà máy dầu khí/ hóa dầu/ năng lượng 6 đến 8 m/giờ Chế biến thịt/mỡ 5 đến 7 m/giờ Nhà máy gia cầm/sữa 4 đến 6 m/giờ Ngành công nghiệp giấy và bột giấy 5 đến 6 m/giờ Xử lý nước thải đô thị đến 12 m/giờ Tỷ lệ tải trọng chất rắn (SLR) Tỷ lệ tải trọng chất rắn là tốc độ của tổng các chất rắn và FOG trong dòng chảy đến ảnh hưởng đến diện tích bề mặt trong bể tuyển nổi. Đơn vị là khối lượng trên một đơn vị diện tích trên một đone vị thời gian. SLR thiết kế trung bình khoảng từ 4 kg/m2.giờ lên đến 18 kg/m2.giờ với hóa chất. Nhìn chung, tăng SLR sẽ làm giảm nồng độ nổi. Hệ thống tuyển nổi áp lực. Các hệ thống phổ biến nhất hiện nay là sản xuất đơn vị hình chữ nhật bằng cách sử dụng áp suất cao để cung cấp không khí hòa tan khuyến khích tuyển nổi. Như minh họa trong hình 9, một hệ thống DAF bao gồm các chính sau đây thành phần: Hình 9. Bộ phận chính cùa DAF Sự liên thông giữa các ngăn hoặc buồng tuyển nổi. Giúp cho sự pha trộn của không khí hòa tan với dòng nước vào cho phép các bong bóng đính kèm vào hạt keo tụ. Ngoài ra thậm chí cung cấp phân phối các dòng chảy theo chiều ngang của các đơn vị. Buồng tuyển nổi cung cấp diện tích bề mặt nổi cho không khí hòa tan và các hạt keo tụ. Hệ thống sử dụng việc sử dụng các tấm nghiêng để làm tăng thêm sự phân chia chất rắn trong nước thải với các đặc tính nhất định. Gàu xúc bọt bề mặt: Là phương tiện để loại bỏ các hạt keo tụ nổi để chuyển khử nước hoặc xử lí khác. Các hệ thống phổ biến nhất được sử dụng liên quan đến một loạt các lần kéo để gạt bọt bởi một hệ thống ổ đĩa xích với biến tốc độ, ổ đĩa bộ đếm thời gian vận hành. Phần cuối cùng của gàu xúc bọt bề mặt hoặc khoan. Giúp cho việc loại bỏ các chất rắn ở dưới cùng của đơn vị. Nước thải xả vào vách ngăn buồng.Cho phép tách vật chất của nước làm rõ từ hạt keo tụ và đáy trước khi xả từ các đơn vị thông qua các đập tràn hoặc cấu trúc tương tự. Hệ thống không khí bão hòa. Cung cấp lượng không khí cần thiết trong các hình thức thích hợp (kích thước bong bóng trong khoảng 10-100m), tốt nhất là sử dụng dòng tái chế tối thiểu. Các hệ thống không khí bão hòa sử dụng bơm áp suất cao để đẩy không khí vào trong dung dịch với một trong hai dòng chảy đến hoặc một dòng rác thải làm rõ. Giải pháp máy nước là sau đó đưa vào dòng nước thải đến để khuyến khích liên kết bong bóng rắn và tuyển nổi. Trong khi các đơn vị DAF là trung tâm của một thiết kế hệ thống DAF, có một số khác hỗ trợ các hệ thống quan trọng đối với hoạt động DAF tối ưu. Một số trong các hệ thống được thể hiện trong Hình 10, một thiết kế quá trình DAF điển hình: Hình 10. Một thiết kế quá trình DAF điển hình Sàng lọc. Mặc dù thỉnh thoảng bị bỏ qua bởi các nhà thiết kế, kiểm tra thích hợp lớn chất rắn (ví dụ, các chất rắn sản phẩm, thùng rác) từ nước thải công nghiệp làm giảm chất rắn trên DAF, có thể cải thiện điều hóa hạ lưu, và làm giảm bảo trì yêu cầu do bị tắc van, máy bơm, và đường ống. Thiết bị hiệu chỉnh làm cân bằng thích hợp của nước thải công nghiệp có thể cung cấp thường xuyên hơn và dòng đồng nhất để các đơn vị DAF. Điều này có thể nâng cao hiệu quả của quá trình hóa học được sử dụng để làm đông và kết bông trước khi tuyển nổi. Ngoài ra, cân bằng thủy lực làm giảm sự tăng cao có thể gây hại đến hiệu suất của hệ thống. Hầu hết các hóa chất được sử dụng hoặc kết bông trong ống, bể tuyển nổi và được cho vào trong quá trình dòng chảy. Những hệ thống này phải được thiết kế để cung cấp lượng thời gian thích hợp và pha trộn năng lượng cho chương trình hóa học được sử dụng. Ngoài ra, kiểm soát pH chính xác thường sẽ cải thiện hiệu suất của hầu hết các quá trình hóa học. Xử lí bọt bề mặt. Các hóa chất điều chỉnh độ pH, chất keo tụ, và polyme được sử dụng trong một quá trình hóa học sẽ ảnh hưởng đến các phương thức xử lý hoặc bọt bề mặt được tạo ra bởi hệ thống DAF. Độ ẩm và khối lượng của vật liệu phục hồi bằng một hệ thống khác nhau và phải được xem xét khi định cỡ bơm chuyển, bể chứa và các hệ thống khử nước. Quá trình keo tụ và tạo bông là cần thiết cho giai đoạn tiền xử lý. Sự keo tụ là bước thêm vào hóa chất. Chất keo tụ được sử dụng hầu hết trong xử lý nước thải có nhôm và muối sắt. Quá trình keo tụ có hai mục đích: để làm mất ổn định các hạt có trong nước thô và chuyển đổi các chất hữu cơ tự nhiên hòa tan thành các hạt. Mục đích thứ hai, trong vòn 25 năm qua, keo tụ đã trở thành một phần thiết yếu của xử lý nước được sử dụng để có thể loại bỏ càng nhiều cacbon hữu cơ. Việc lựa chọn liều lượng và điều kiện pH của chất keo tụ một cách thích hợp để hình thành nên các hạt trong nước thô và các hạt mới được hình thành thông qua sự kết tủa kim loại, đó có thể là các cụm xốp ở trong bể tạo bông, và cuối cùng là để các bọt khí có thể bám vào. Mục tiêu của hóa chất keo tụ là để tạo ra các hạt có ít hoặc không tích điện bề mặt và đặc tính kỵ nước tương đối. Các chất hóa học keo tụ cho sự lắng và thiết bị DAF tương tự, do đó liều lượng chất keo tụ và điều kiện pH là giống nhau để hình thành cụm xốp. Ngoại lệ là đối với một số loại nước, đặc biệt là nước có độ đục thấp, các công trình lắng có thể yêu cầu liều lượng keo tụ cao hơn để tăng động lực học chất keo và hình thành cụm xốp đủ lớn để quá trình xảy ra nhanh chóng. Hình 11. Sơ đồ quy trình của công trình xử lý nước bằng phương pháp tuyển nổi áp lực Bước kết bông liên quan đến việc khuấy trộn của nước để tạo ra sự va chạm và kết bông giữa các hạt. Kích thước của các cụm xốp ở đầu vào đến bể tuyển nổi ảnh hưởng lớn đến sự va chạm giữa các bọt khí và cụm xốp trong vùng tiếp xúc của bể tuyển nổi, và sau đó tăng vận tốc va chạm của các cụm xốp với bọt khí trong vùng phân tách của bể tuyển nổi. Kết bông được sử dụng ở hai quá trình lắng và tuyển nổi, nhưng với mục đích khác nhau. Sau quá trình lắng của kết bông, mục đích là để tạo ra các cụm xốp lớn có thể lắng với tốc độ nhanh chóng. Cụm xốp có kích thước 100µm hoặc lớn hơn được yêu cầu để tạo ra tỷ lệ lắng phù hợp. Kích thước cụm xốp thích hợp cho DAF khác nhau, đặc biệt là trong xử lý nước cung cấp cho bể chứa với mật độ của các hạt thấp và độ đục nhỏ. Đối với xử lý nước cho các loại cung cấp, kích thước tối ưu của các cum xốp trong vùng tiếp xúc của bể tuyển nổi là 10s của µm được xác định từ mô hình, phòng thí nghiệm, và dữ liệu công trình thí điểm (Edzwald et al. 1990; Edzwald and Wingler 1990; Edzwald et al. 1992; Edzwald 1995). Nó được chứng minh thông qua việc mở rộng dữ liệu công trình thí điểm rằng thời gian đủ để quá trình kết bông diễn ra là 5-10 phút (Valade et al . 1996; Edzwald et al. 1999). Trong 10 đến 15 năm qua, nhiều công trình kích thước thực trên toàn thế giới đã được đặt vào hoạt động với thời gian kết bông ngắn. Một nhà máy DAF lớn(1.1x106 m3/d) với thời gian kết bông là 5 phút được xây dựng cho thành phố New York. Bể DAF được chia thành 2 phần với chức năng khác nhau được minh họa ở hình 10. Vùng tiếp xúc, nơi mà các cụm xốp được đưa vào và tiếp xúc với bọt khí. Tại đây, diễn ra sự va chạm giữa các bọt khí và cụm xốp. Nếu các hạt kết bông được chuẩn bị tốt qua quá trình keo tụ về mặt hóa chất, sau đó các bọt khí va chạm với cụm xốp có liên quan đến sản lượng hỗn hộp khí-cặn. Nước mang theo hỗn hợp khí-cặn lở lửng đến phần thứ hai của bể, được gọi là vùng phân tách. Ở đây, các bọt khí chưa dính bám vào cum xốp và hỗn hợp khí-cặn có thể nổi lên bề mặt của bể. Lớp váng trên bề mặt của bể bao gồm bọt khí và hỗn hợp của bọt khí gắn với cụm xốp. Trong ứng dụng cho nước cấp, bọt này được gọi là phao. Theo thời gian, lớp phao này được thu thấp và thải bỏ khỏi bể. Nước đã qua xử lý được rút ra từ dưới đáy bể. Trong một số ứng dụng, DAF được đặt trước bộ lọc. Không khí được hòa tan trong dòng chảy tuần hoàn bằng cách thêm không khí dưới áp lực trong bình áp lực. Tỷ số tuần hoàn (R) được xác định bởi Eq.1, trong đó Q là dòng chảy vào hệ thống và Qr là dòng chảy tuần hoàn. Tỷ lệ tuần hoàn là từ 8 đến 12%. Áp suất của bình áp lực từ 400 đến 600 kPa. Dòng chảy tuần hoàn được đưa vào bằng vòi phun hoặc van đặc biết ở lối vào phía dưới của vùng tiếp xúc. Các bọt khí nhỏ có kích thước từ 10 đến 100 µm được sản xuất và cung cấp cho sự xuất hiện màu trắng sữa của nước; do đó có tên là nước trắng. R=QrQ (1) Một số ý kiến giới thiệu được thực hiện về tải trọng thủy lực của bể DAF. Thông thường, việc tải trọng thủy lực (Vnom-hl) được sử dụng để mô tả DAF. Nó được định nghĩa bởi Eq.(2). Chú ý rằng định nghĩa này bỏ qua các dòng chảy tuần hoàn và sử dụng toàn bộ khu vực bể (A) của vùng tiếp xúc và vùng phân tách. Vnom-hl=QA (2) Việc loại bỏ bọt khí và hỗn hợp khí-cặn xảy ra trong vùng phân tách. Sự tách biệt của bọt khí và hỗn hợp phụ thuộc vào việc tăng vận tốc liên quan đến tải trọng thủy lực của vùng phân tách phải lớn. Vì vậy, việc thực hiện vùng phân tách phải được miêu tả với tải trọng thủy lực (vsz-hl) sử dụng tổng của các dòng chảy thông qua thiết bị và dòng chảy tuần hoàn được tách bởi khu vực phân tách (Asz) được trình bày bởi Eq.(3) vsz-hl=Q+ QrAsz (3) Thiết kế tuyển nổi áp lực Ba thông số thiết kế tuyển nổi áp lực quan trọng đối với thành công của việc sục khí vào nước thải đã được mô tả. Hiện nay, các nhà quản lý nước thải và kỹ thuật viên thường xuyên gặp phải những vấn đề trong xử lý nước. Những vấn đề như vậy có thể cải thiện hiệu suất của hệ thống tuyển nổi áp lực hoặc giúp lựa chọn một đơn vị mới. Thông qua ứng dụng của các phân tích quan trọng, quản lý và kỹ thuật viên sẽ cảm thấy hiệu quả xử ký nước được cải thiện trong thời gian dài. Bằng cách tìm hiểu các thông số thiết kế, hạn chế các lỗi tiềm tàng có thể tránh được trong thiết kế. Tốc độ tải trọng thủy lực Tốc độ tải trọng thủy lực của một đơn vị DAF được đưa ra như là dòng chảy trong galong trên đơn vị diện tích. Tốc độ tải trọng thủy lực đôi khi còn được gọi là tỷ lệ bề mặt chảy tràn hoặc tỷ lệ chảy tràn thủy lực. Tốc độ tải trọng là một hàm toán học mô tả sự cạnh tranh của hai vận tốc trong bể DAF. Đây là vận tốc ngang của nước và vận tốc theo chiều thẳng đứng của chất rắn lơ lửng trong cột nước. Đây là hình minh họa Hình 1. Hình 12. Tốc độ tải trọng là một hàm của vận tốc ngang của nước và vận tốc thẳng đứng của chất rắn lơ lửng. Các nhà quản lý và kỹ thuật viên có thể đánh giá hiệu suất thủy lực của một hệ thống DAF truyền thống bằng cách làm theo các bước sau. Nhân chiều dài và chiều rộng của bình để tìm diện tích bề mặt. Tiếp theo phân chia tỷ lệ lưu lượng thiết kế của DAF bởi diện tích bề mặt để thiết kế hệ thống cụ thể của tốc độ tải trọng thủy lực. Ví dụ được đưa ra ở đây là dành cho một hệ thống DAF được thiết kế với tỷ lệ nước thải có 125 galong trên phút với 1500 ppm TSS và tuần hoàn 20%. Từ nay, chúng ta có thể đo lường và tính toán nhiều điểm đánh giá đối với các thông số thiết kế DAF như sau: Tỷ lệ tải trọng thủy lực: DAF: Chiều rộng: 6 ft. Chiều dài: 14 ft. Chiều cao: 6 ft Diện tích bề mặt: 6 ft x 14 ft = 84.0 ft2 Tốc độ dòng chảy DAF: 125 gpm + (125 x 20%) = 150 gpm Tốc độ tải trọng thủy lực: 150 gpm ÷ 84.0 ft2 = 1.79 gpm/ft2 Nguyên tắc so sánh: 0.3 gpm/ft2 đến 3.0 gpm/ft2 Cho dù các cuộc thảo luận về tuyển nổi hoặc lắng các chất rắn, một chất rắn có trong nước đi vào hệ thống DAF phải có thời gian để nổi lên bề mặt hoặc chìm xuống đáy trước khi nó được đưa ra khỏi bề cùng với nước thải. Tuyển nổi hoặc lắng được định nghĩa là tỷ lệ tăng hoặc tỷ lệ lắng, như trường hợp có thể. Sau đó hạt có tỷ lệ gia tăng bằng hoặc lớn hơn tốc độ thiết kế của DAF sẽ được loại bỏ trước khi nước thoát ra khỏi bể. Một cách tốt nhất để nhận ra điều này đầu tiên là thử nghiệm trong phòng thí nghiệm, các hạt tăng năng suất bằng cách thu thập các mẫu nước trước khi đưa vào hệ thống DAF và đo lường cụ thể chất rắn tăng tốc ở các bước mỗi phút. Điều này có thể được thực hiện bằng cách chia 1 hoặc 2 lít trong xilanh hoặc máy kiểm soát không khí để mô phỏng DAF. Tiếp theo phân chia dòng chảy DAF thep tỷ ệ tăng của hạt đó để tìm diện tích bề mặt cần thiết cho DAF. So sánh con số đó với diện tích bề mặt thực tế của hệ thống được đánh giá. Diện tích bề mặt được yêu cầu của DAF DAF: Chiều rộng: 6 ft. Chiều dài: 14 ft. Chiều cao: 6 ft Mẫu kiểm tra tỷ lệ tăng trong phòng thí nghiệm: 0.5 ft/phút Tốc độ dòng chảy của DAF: 150 gpm ÷ 7.48 ft3 = 20.05 ft3/phút Diện tích bề mặt yêu cầu: 20.05 ft3/phút ÷ 0.5 ft/phút = 40.1 ft2 Quy luật diện tích bề mặt DAF: yêu cầu tối thiểu 125% Yêu cầu so với thực tế: 40.1 ft2 so với 84.0 ft2 Chúng ta có thể thưc hiện thêm một bước nữa. Theo kinh nghiệm, tỷ lệ tăng hạt phải bằng hoặc lớn hơn chiều cao của bể chia theo thời gian lưu nước của bể. Một so sánh trực tiếp của việc tăng năng suất các hạt so với tỷ lệ tăng thiết kế của bể DAF cũng là công cụ đánh giá có giá trị. Kiểm tra tốc độ gia tăng DAF: Chiều rộng: 6 ft. Chiều dài: 14 ft. Chiều cao: 6 ft Khối lượng DAF: 6 ft x 14 ft x 6 ft x 7.48 g/ft3 = 3,770 galong Mẫu kiểm tra tỷ lệ tăng trong phòng thí nghiệm: 0.5 ft/phút Thời gian lưu trong DAF: 3,770 galong ÷ 150 gpm = 25.1 phút Tỷ lệ tăng DAF: 6 ft chiều cao ÷ 25.1 phút = 0.24 ft/phút Mẫu so với thực tế: 0.5 ft/phút so với 0.24 ft Để đặt một điểm tốt hơn vấn đề này, bất kỳ hạt rắn nào với tỷ lệ tăng từ 0.24 ft/phút hoặc lớn hơn sẽ nổi lên bề mặt của bể DAF và được gạt ra bởi dây chuyền các cánh gạn bọt. Mục tiêu không vượt quá tốc độ tải trọng thủy lực của DAF và cản trở quá trình đó. Tốc độ tải trọng chất rắn Cũng giống như tốc độ tải trọng thủy lực, tốc độ tải trọng chất rắn được tính như một pao chất rắn trên mỗi diện tích vuông bề mặt DAF trong mỗi giờ hoạt động. Về cơ bản, có một giới hạn về số lượng chất rắn có thể tích tụ trên bề mặt của DAF trước khi hiệu suất giảm đi. Tốc độ tải trọng chất rắn DAF: Chiều rộng: 6 ft. Chiều dài: 14 ft. Chiều cao: 6 ft Diện tích bề mặt: 6 ft x 14 ft = 84.0 ft2 Tải trọng TSS trong DAF: (1,500 ppm x 125 gpm x 8.34) ÷ 1,000,000 ÷ 84.0 ft2 = 0.019 lít/ft2/phút Tải trọng bề mặt: 0.019 lít/ft2/phút x 60 = 1.14 lít/ft2/giờ Nguyên tắc so sánh: 1.0 lít/ft2/giờ so với 6.0 lít/ft2/giờ Một hệ thống hoạt động tối ưu sẽ tích lũy chất rắn đồng đều trên bề mặt DAF. Các chất rắn sẽ xây dựng một khối chặt chẽ và ngày càng dày lên. Các chất rắn sẽ được lấy ra tại một điểm trước khi khối lượng của chúng giống như các hạt được lấy ra khỏi đáy của lớp phủ và thoát ra cùng với nước thải. Tỷ lệ rắn-khí Tỷ lệ khí-rắn được tính toán với lượng khí áp dụng cho một khối lượng chất rắn nhất định trong quá trình DAF. Giá trị này được thể hiện một pao không khí với pao chất rắn. Lượng không khí cần thiết cho hoạt động thay đổi hiệu suất của DAF do đặc điểm thiết kế riêng của DAF và từ dòng thải này đến dòng thải khác chủ yếu là do các chất rắn lơ lửng. Tuy nhiên, các thiết bị để hút không khí trong nước là cho một cuộc thảo luận. Công thức tỷ lệ khí-rắn: AS=1.3 × Sa P-1×RSS ×Q Sa: độ hòa tan của không khí P : áp suất khí quyển ở 20oC SS : chất rắn lơ lửng ppm R : Tỷ lệ tuần hoàn gpm Q : nước cung cấp cho DAF gpm Tỷ lệ khí-rắn Dòng chảy của DAF: 125 gpm Tỷ lệ tuần hoàn không khí : 20% Tải trọng TSS trong DAF: 1,500 ppm Nguyên tắc so sánh: 0.005 lít với 0.06 lít AS=1.3 × 15.7 18.7-1×251,500 ×125=0.048 lít không khí trên pao chất rắn Ứng dụng Trong năm đến mười năm qua việc cải thiện thiết bị DAF để DAF có thể được thiết kế và hoạt động ở mức 20 đến 40 m/h với việc loại bỏ tuyêt vời độ đục hoặc các hạt ít hoặc không có mang theo bọt khí. Một hệ thống được phát triển bởi Rictor Oy (Phần Lan) và được sử dụng ở một số nhà máy nước cấp. Một thiết bị lưu ý ở Tampere (Phần Lan) được thiết kế vào khoảng 40 m/h. Công nghệ của Rictor có sẵn để sử dụng cho toàn thê giới bởi giấy phép của Infilco Degrémont. Nó được biết đến với tên thương mại là AquaDAFTM. Ở Mỹ có nhà máy ở New York và California được thiết kế ít nhất là 30 m/h. Được thể hiện ở hình đầu tiên của hình 13. Bể DAF hoạt động ở tốc độ cao với cải thiện dòng chảy thủy lực qua bể so với nhiều bể thông thường. Một phát triển quan trọng là tấm sàn lỗ ở dưới đáy bể DAF phân phối dòng chảy tốt hơn trong khu phân tách và tại các cửa ra thông qua các tấm sàn. (a) (b) Hình 13. Hệ thống DAF tốc độ cao. Hình trên: AquaDAFTM Infilco Degrémont (cống hiến của Bob Raczka, United Water), lưu ý tấm sàn lỗ; Hình dưới: DAFRapide® (Cống hiến của Purac Ltd.), lưu ý ống hoặc tấm sàn. Amato et al.(2001) và Dahlquist và Göransson (2004) đã báo cáo về sự phát triển và ứng dụng của quá trình DAF tốc độ cao, được gọi là DAFRapide® được phát triển bởi Purac Ltd. (Anh) and Purac AB (Thụy Điển). DAFRapide® được thiết kế với tải trọng thủy lực cao tối đa khoảng 40 m/h, như mô tả ở hình 13b. Các ống hoặc tấm được đặt bên trong bể DAF để cải thiện việc phân phối dòng chảy thủy lực và tăng diện tích khu vực tách biệt để loại bỏ hỗn hợp khi-cặn và bọt khí tự do. Một ứng dụng khác của bể DAFRapide® là có thể ứng dụng tốt trong xử lý nước cấp với thời gian kết bông ngắn khoảng 5 phút. Cuối cùng, trong năm qua, công ty Leopold đã giới thiệu một quá trình DAF tốc độ cao được gọi là Clari-DAFTM. Hệ thống tuyển nổi áp lực Napier Ried’s “DIFLOATTM” Hệ thống Napier Ried’s “DIFLOATTM” DAF loại bỏ tổng chất rắn lơ lửng (TSS); tảo, chất béo, dầu và mỡ (FOG); nhu cầu oxy sinh hóa (BOD) và nhu cầu oxy hóa học (COD) từ nước và nước thải. Hệ thống DIFLOATTM được sử dụng như một thiết bị lắng và cũng là một thiết bị cô đặc bùn. Hình 14. Sơ đồ phác họa của bể DAF Kết luận. Tuyển nổi áp lực (DAF) là một công nghệ vật lý/ hóa học đã được chứng minh và hiệu quả cho việc xử lý nước thải công nghiệp, nước thải đô thị và các dòng thải khác. DAF đã chứng minh được hiệu quả của công nghệ tiền xử lý bằng cách giảm tải lượng thực phẩm hữu cơ trong nước thải. Công nghệ DAF đã được sử dụng rộng rãi trong xử lý nước thải nhà máy lọc dầu và ngành công nghiệp khai thác mỏ. Trong cả hai trường hợp, DAF kết hợp với keo tụ hóa học đã được chứng minh là rất hiệu quả trong việc loại bỏ các hạt từ nước thải. Hệ thống DAF đáp ứng các mục tiêu xử lý bao gồm:Sản phẩm phục hồi và tái sử dụng, tiền xử lý nước thải cống rãnh, tiền xử lý để giảm tải trên các hệ thống xử lý sinh học ở hạ lưu, làm sạch dòng chảy xử lý sinh học, làm dày chất rắn sinh học. Có một loạt các ứng dụng của DAF trong xử lý nước thải công nghiệp và nước thải đô thị gồm: có chế biến gia cầm, chế biến thịt, dệt may, chế biến trứng, giấy và bột giấy, sữa và sản phẩm của sữa, xi mạ kim loại, banh kẹo, chế biến thực phẩm, dầu khí và lọc hóa dầu, khí tự nhiên và dầu mỏ, sinh hóa, xử lý chất thải bùn dày, loại bỏ phốt pho, loại bỏ tảo,... Như vậy, DAF không được xem như một quá trình riêng biệt, nhưng được tích hợp vào thiết kế và hoạt động của hệ thống xử lý tổng thể. Tiến bộ công nghệ gần đây trong DAF bao gồm DAFRapide, AquaDAF và DAF tỷ lệ cao. DAF được xem như là một trong những công cụ mạnh mẽ nhất trong việc loại bỏ những nhóm hạt keo lơ lửng khó xử lý, kết tủa hoặc phân tán tốt. Tài liệu tham khảo [1] Effect Of Using Dissolved Air Flotation System On Industrial Wastewater Treatment In Pilot Scale, Yahya Habibzadeh*, K.B.Gurbanvo** [2] Pollution Engineering, November 2010. Pollution Control Solutions For Air, Water, Solid & Hazardous Waste [3] ReThinKing Disolved Air Flotation (DAF) Design For Industrial Pretreatment [4] Developments of High Rate Dissolved Air Flotation for Drinking Water Treatment, James K. Edzwald Department of Civil and Environmental Engineering University of Massachusetts Amherst, MA 01003 USA [5] Dissolved Air Flotation In Industrial Wastewater Treatment [6] Optimizing the Air Dissolution Parameters in an Unpacked Dissolved Air Flotation System, Adam Dassey 1,2 and Chandra Theegala 1,2,*
File đính kèm:
tieu_luan_cong_nghe_tuyen_noi_ap_luc_trong_xu_ly_nuoc_thai.docx